Large bathroom & kitchen furniture manufacturer transitions from Solvent to Water-Based Coatings
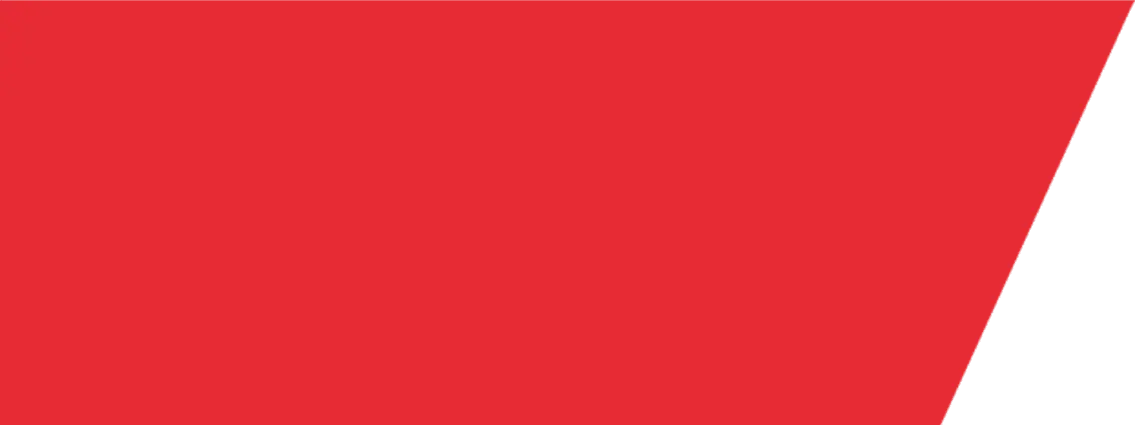
Client overview
A prominent bathroom and kitchen furniture manufacturer and fabricators of solid surfaces located in the Midlands, renowned for their high-quality kitchen cabinets and furniture wanted to realign their manufacturing to match their corporate social responsibility policy and environmental impact by complying with stringent environmental regulations. Their traditional use of solvent-based coatings was not only harmful to the environment but also posed health risks to their employees. The company sought a sustainable alternative that would maintain their product quality while enhancing worker safety and reducing environmental footprint.
Objectives
- Environmental Compliance: Transition from solvent-based to water-based coatings to meet environmental regulations and reduce VOCs, ensuring compliance with current and future standards.
- Waste Disposal & Health and Safety: Address waste disposal challenges and improve health and safety conditions.
- Cost Savings and Efficiency: Achieve cost savings and improve paint utilisation for more efficient operations.
- Maintain Quality: Ensure the new coating delivers the high-quality finish that customers expect.
- Minimise Disruption: Implement the new system with minimal disruption to ongoing production processes.
- Commercial Benefits: Highlight several commercial benefits of transitioning from solvent-based to water-based coatings, such as lower insurance premiums and the elimination of certain training requirements.
- Increased Throughput: Introduce a new automatic spray line to accommodate increased capacity and demand.

Solution
Intercoat Paints proposed their Aqualine+ range of water-based coatings as the ideal solution. This product line promised excellent durability, aesthetic appeal, and environmental benefits.
Phase 1: Initial Assessment and Planning
Intercoat Paints’ technical team began by conducting an in-depth assessment of the manufacturer’s current coating processes, equipment, and production lines. This phase involved:
We wanted to weigh up objectives against his new process:
- Analysing the specific requirements of the kitchen manufacturer’s products.
- Identifying any potential challenges in transitioning from solvent-based to water-based coatings.
- Developing a detailed implementation plan to ensure a seamless transition.
Within 2 months, Intercoat Paints’ technical team worked with the clients technical team manufactures product management team. Key activities during this period included:
Intercoat worked closely with the manufacturer and the new paint line supplier by going out to Italy and identifying which spray equipment manufacturer would meet the customers criteria
Once a decision was made on who will manufacture the line, Intercoat’s technical took paint over to Italy to run some ran trials on a demo line. Aqualine+ coating worked without any modification and the trial was a success. Within a 2-3 three-hour window a satisfactory set of wooden components were generated.
Installation of the new paint line
- Pilot Testing: Conducting pilot runs to test the Aqualine+ coatings on various kitchen products. This helped in fine-tuning the application process and ensuring the coatings met the desired quality standards.
- Training and Support: Providing initial training for the manufacturer’s staff on the application and handling of Aqualine+.
Phase 3: Full-Scale Implementation
- After successful pilot testing and staff training, the full-scale production was rolled out across multiple paint colours within the manufacturer’s facility. Key aspects of this phase included:
- Continuous Monitoring: The technical team from Intercoat Paints closely monitored the initial production runs to ensure everything operated smoothly and any issues were promptly addressed.
- Ongoing Support: Regular follow-up visits and on-call support were provided to assist with any technical challenges and ensure consistent product quality.
Results
- Successful Transition: The manufacturer successfully transitioned from solvent-based to water-based coatings without any significant disruptions to their production schedule.
- Environmental Benefits: The switch to Aqualine+ water-based coatings resulted in a substantial reduction in VOC emissions, contributing to a healthier work environment and compliance with environmental regulations. Reduction in waste disposal costs.
- Commercial Benefits – Reduction in insurance costs and elimination of certain training programs as required by traditional Solvent based products.
- Quality Maintenance: The Aqualine+ range delivered a high-quality finish that met the manufacturer’s standards, maintaining the aesthetic and durability that their customers expect.
- Enhanced Production: The Paint line is now efficiently utilising the Aqualine+ range, which due to its enhanced drying times has increased productivity supporting increased level of manufacturing and enabling the manufacturer to continue delivering top-quality products.
Colin Tilly Technical Services Manager comments “The collaboration between Intercoat Paints and our customer in the Midlands stands as a testament to the successful integration of sustainable practices in industrial production. Through comprehensive support and innovative solutions by the use of Aqualine+. Intercoat Paints facilitated a seamless transition that not only met environmental and safety standards but also maintained the high quality of the manufacturer’s products. This case exemplifies how industry partnerships can drive significant advancements in manufacturing processes and sustainability”